Custom Thermoforming Solutions Tailored to Your Needs by INPAK
In today’s competitive manufacturing environment, businesses demand packaging solutions that are not only efficient but also customizable to their unique product requirements. This is where custom thermoforming steps in, offering unparalleled flexibility and precision in plastic packaging production. INPAK stands as a trusted leader in providing tailor-made thermoforming machines that meet diverse industrial needs. Whether for food packaging or industrial applications, INPAK’s innovative technology ensures high-quality output with consistent performance.
Table of Contents
Custom thermoforming is a process that allows companies to design packaging that perfectly fits their product specifications, enhancing both product protection and shelf appeal. With rising consumer expectations and increasingly stringent regulatory standards, adopting bespoke plastic packaging machines has become essential for manufacturers aiming to differentiate themselves. INPAK’s dedication to advanced engineering and customer-centric solutions enables businesses to optimize their production lines with machines built for precision and adaptability.
The integration of thermoforming machine manufacturing expertise with a focus on sustainability and efficiency makes INPAK a preferred thermoforming machine supplier globally. Their solutions cater to a wide range of industries, from food to medical packaging, supporting companies in achieving superior packaging quality while reducing waste and operational costs. Choosing INPAK means investing in reliable, cost-effective, and energy-efficient equipment designed to elevate production standards.
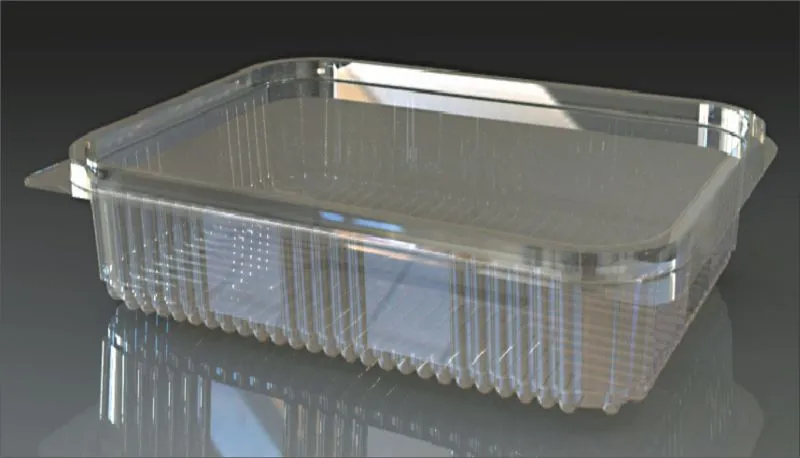
Custom Thermoforming Solutions Tailored to Your Needs by INPAK
What is Thermoforming and How Does It Work?
Thermoforming is a manufacturing process where a plastic sheet is heated to a pliable forming temperature, then shaped into a specific mold and cooled to retain that shape. This technique is widely used to create packaging materials such as trays, containers, lids, and blisters, offering versatility across numerous industries. The process begins by feeding the plastic sheet into the thermoforming machine, where it is heated evenly to ensure optimal formability.
Once the sheet reaches the desired temperature, it is either vacuum-formed or pressure-formed onto the mold, depending on the design requirements. Vacuum forming involves pulling the heated plastic tightly over the mold using suction, while pressure forming adds additional air pressure to achieve finer details and deeper draws. The formed plastic is then cooled quickly, solidifying into its final shape before being trimmed to create the finished product.
The efficiency and precision of thermoforming machine production allow manufacturers to achieve consistent and high-quality packaging outputs. This process supports a wide variety of materials including PET, PP, PVC, and biodegradable alternatives, making it a sustainable choice in plastic packaging machines. INPAK’s machines excel in delivering repeatable accuracy, essential for custom packaging applications that require exact dimensions and structural integrity.
Advantages of Custom Thermoforming in Industrial Production
Custom thermoforming offers significant benefits for industrial production, providing manufacturers with the flexibility to create packaging solutions tailored precisely to their product’s needs. One of the primary advantages is the ability to optimize material usage, reducing waste and lowering overall production costs. Unlike generic packaging, custom thermoformed products minimize excess material while enhancing durability, which is particularly important for food and medical packaging.
Additionally, custom solutions improve product protection and presentation. By designing packaging that fits snugly around the product, companies can enhance safety during transport and extend shelf life. The aesthetic customization also allows brands to create unique packaging that attracts consumers, helping products stand out in competitive retail environments. This level of customization is only achievable through advanced thermoforming machine manufacturing processes.
The adaptability of custom thermoforming machines further supports scalability and production efficiency. INPAK’s machines are engineered to handle different mold sizes and materials without sacrificing speed or quality, enabling businesses to quickly adapt to changing market demands. Moreover, the precision and automation features reduce labor costs and increase throughput, making custom thermoforming an ideal solution for businesses aiming to balance quality with cost-effectiveness.
Types of Thermoforming Machines: Which One Do You Need?
The selection of the right thermoforming machine depends largely on your product’s packaging requirements and production volume. There are several types of thermoforming machines, each offering unique capabilities. Basic vacuum forming machines use suction to pull heated plastic over a mold, suitable for simpler shapes and lower production runs. These machines are cost-effective and ideal for companies starting in thermoforming.
Pressure forming machines combine vacuum with additional air pressure to achieve greater detail and depth in the packaging. This type is preferred when producing complex designs requiring fine contours and superior surface quality. For high-volume industrial production, rotary and inline thermoforming machines provide continuous and automated operations, optimizing throughput and minimizing downtime.
INPAK offers a wide range of thermoforming machines from entry-level to advanced models such as the TSR-800, TS-850, and TS-1000, catering to diverse industry needs. Their machines incorporate the latest technology like servo-driven chains and variable heating systems to ensure precision and efficiency. Evaluating your packaging complexity, material compatibility, and production targets will guide you to select the best equipment for your business.
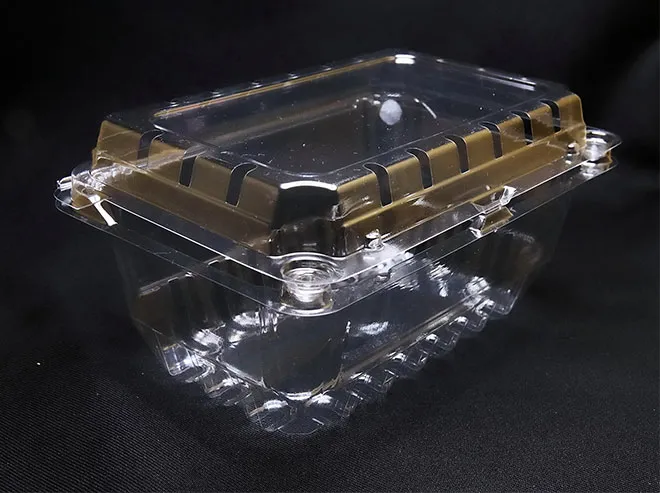
Custom Thermoforming Solutions Tailored to Your Needs by INPAK
Materials Used in Thermoforming and Their Properties
The choice of materials is crucial in thermoforming machine production as it affects the final product’s durability, appearance, and environmental impact. Common materials used include PET, CPET, PP, PVC, PS, OPS, and PLA, each offering distinct properties suited to specific applications. PET is widely favored in food packaging for its clarity, strength, and recyclability, while CPET is suitable for heat-resistant containers like ready meal trays.
PP is valued for its chemical resistance and flexibility, making it popular in medical and industrial packaging. PVC offers excellent transparency and impact resistance but has environmental concerns which lead some manufacturers to seek alternatives. PS and OPS are lightweight and cost-effective options often used in disposable trays and lids. PLA, a biodegradable polymer, is gaining traction due to its sustainable nature and compostability.
INPAK’s plastic packaging machines are designed to handle this wide spectrum of materials, allowing manufacturers to select substrates that meet their performance and sustainability goals. Their machines’ advanced heating and forming technologies ensure optimal material distribution and product consistency regardless of the plastic type used.
Choosing the Right Thermoforming Equipment for Your Business
Selecting the appropriate thermoforming machine supplier and equipment is critical to maximizing production efficiency and achieving desired packaging outcomes. Factors to consider include production capacity, material compatibility, automation features, and after-sales support. It is essential to partner with manufacturers who provide customized solutions tailored to your specific packaging needs.
INPAK stands out as a professional thermoforming machine manufacturer offering a comprehensive portfolio of machines equipped with advanced human-machine interfaces and remote access capabilities. Their machines come with features like automatic lubrication, servo plug assists, and variable stacking options, ensuring smooth operation and minimal downtime. These innovations help businesses reduce operational costs while maintaining high product quality.
Furthermore, the ability to integrate additional systems such as pre-heaters and conveyor elevators enhances workflow efficiency. INPAK also provides expert technical support and training, enabling clients to optimize machine performance. Investing in the right thermoforming equipment from a trusted supplier like INPAK guarantees a competitive edge in the evolving packaging industry.
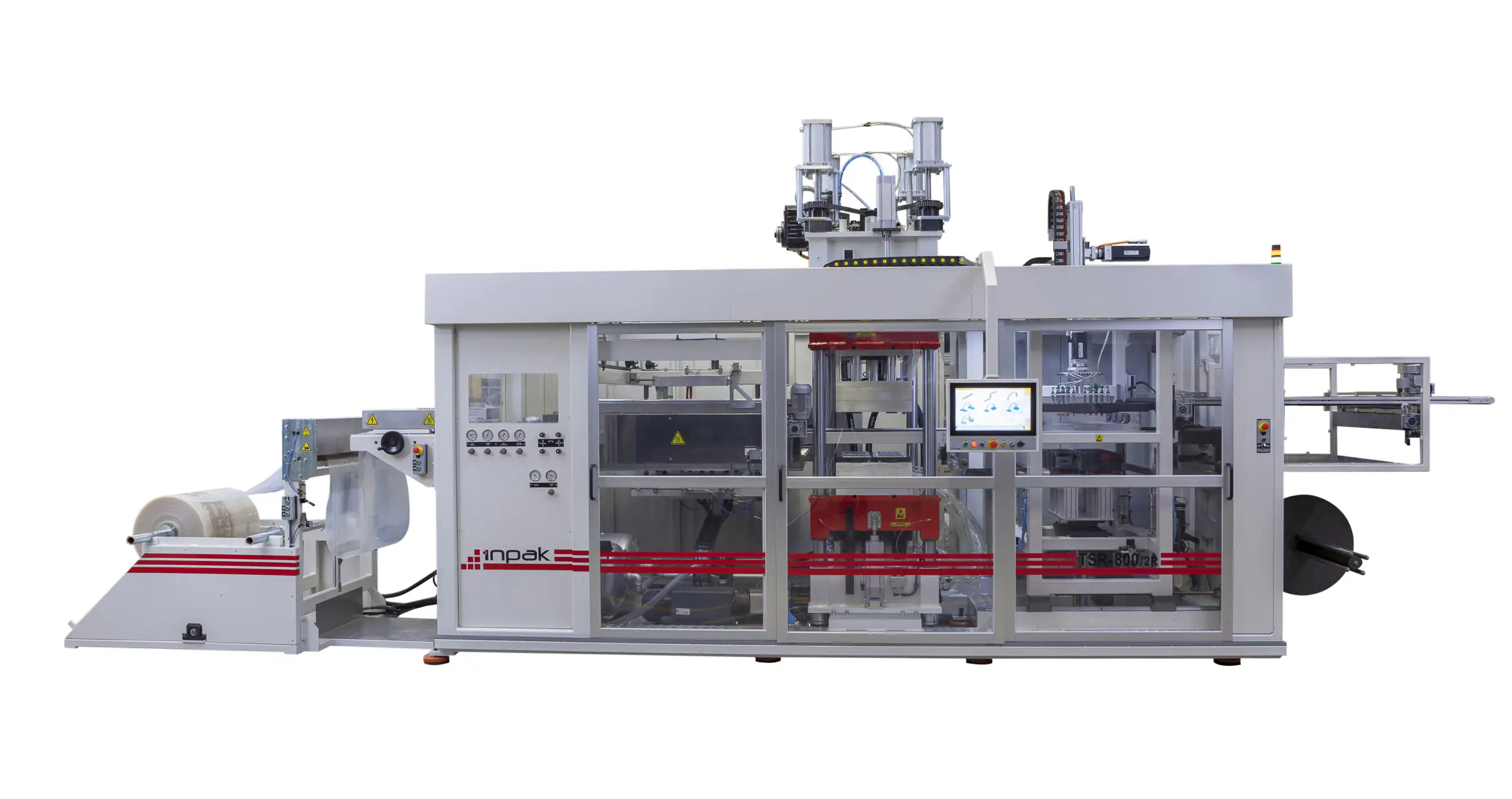
Custom Thermoforming Solutions Tailored to Your Needs by INPAK
INPAK: Professional Thermoforming Machine Solutions
INPAK has established itself as a premier thermoforming machine manufacturer dedicated to innovation and customer satisfaction. Their machines are engineered for versatility, energy efficiency, and durability, making them suitable for diverse industries including food, medical, and industrial packaging sectors. By combining cutting-edge technology with precision engineering, INPAK delivers equipment that consistently meets the highest standards.
One of INPAK’s key strengths lies in its tailored approach to thermoforming machine production, enabling clients to specify machine features and configurations that perfectly align with their operational goals. Their product range includes not only thermoforming machines but also integrated systems like pre-heaters and conveyor elevators, providing complete packaging line solutions. This comprehensive offering simplifies production processes and reduces setup times.
Moreover, INPAK prioritizes sustainability and cost-effectiveness, designing machines that minimize energy consumption and material waste. Their commitment to quality, combined with robust after-sales service and global support network, makes INPAK a reliable partner for businesses looking to innovate and grow in the plastic packaging market. Choosing INPAK means investing in future-proof thermoforming technology tailored to your unique needs.